![]() |
The Beadsmith Needle Files - Set Of 12 - Wire Wrapping! SKU: XTL-2212 $8.29 |
![]() |
The Beadsmith Jewelry Wire Side Cutters, Nippers, Pliers SKU: XTL-5515 $9.99 |
![]() |
E6000 Industrial Strength Glue Adhesive (1 Oz) SKU: XTL-1051 $6.99 |
Hi. This is Julie with Beadaholique.com and I'm going to show you how to remove the back shank off of a button. Buttons are great for using in jewelry making. They offer a really unique element and a lot of possibilities. Here I have a couple projects that have been completed with buttons. I have these clip-on earrings which actually take on a little bit of a retro vintage vibe. This was a skull button. I have a steampunk ring. I've taken a shank off of the backside here and just sanded it flat and put on a glue on ring base to it. That's what I want to do in this project here. I want to take this button and remove that shank and then glue it onto my ring form. So the tools you're going to need are a pair of wire cutters. I actually recommend using a pair that's your household utility wire cutters. I don't want anyone using their nice flush cutters. It will destroy them. So bewarned of that. So use an inexpensive household pair. I would actually rather not be using these but these are what we have on hand. So I'm going to use them for the demonstration. Just remember the older, the cruddier the pair the better. You're going to need a file. I have my diamond file set right here. So I've taken out a file that I want to use. You're going to need a dust mask. I got this at a painting store painting store, hardware store. You're definitely going to want to don that. You're also going to want some safety goggles because when you're snipping off that backside it has a tendency to fly. So I'm going to put on my googles. In one moment I'm going to put on my mask but first I'm going to walk you through the different types of buttons. Here I have a beautiful czech glass button. Now it also has a glass shank which unfortunately means you're kinda stuck. You're not going to be able to snip this off and remove it. It's going to cause the glass to shatter. You're going to end up with glass shards. It's not a good thing. So you can do wonderful things with this button. You'll just have to work around the fact that the shank is going to be attach still. So you can do a bead weaving bezel setting. You can do a lot of different things you can build up the base so that it becomes level with the actual tip of the shank instead of the back side of the button. So on glass ones you just can't remove them. There are some buttons that look like this in the back. This here's a vintage button. What you can do with these is you can go ahead and I'm not going to do it with this button but with just using some pressure go ahead and just try to depress that raised area and often times that's going to collapse down into the button and I always like to use a towel and I like to go ahead and cushion my buttons. It makes a lot easier. It's better on the button too than using it on a hard surface. So another type of button back you're going to run into especially if you're doing vintage buttons are these type right here What you can do is you can snip them right along the edge and then just pull them out. And finally you're going to end up with plastic button shanks and these are actually great. Now I have my safety goggles on so I can feel fine to do this. It looks like metal but it's plastic. What you're going to do is just right up at the edge you can see that my wire cutters are flush against the backside of the button snip and snip Then I'll just file that down. That is basically the same principle I'm going to do with my metal button but it's going to act a little bit differently because it's a lot harder to snip through metal obviously than plastic. So I need to put on my mask. I'll try to talk through the mask. So what you're going to want to do is right here where you see the area widen. So it's pretty much solid metal right along here but then as that loop forms right in there is where you want to snip. Go to the other side. Make sure you have your goggles on. Make sure that you're flat screen TV is not right in front of your work station because this is going to fly. So you want to position in an direction that's not going to be a problem if that little piece goes. You can try to also catch the piece if you want. That way it didn't go quite as far but just be prepared for that. Now I actually have quite a bit of a remnant left of my shank. I'm going to cushion my button face down in the towel. Take my diamond file and I'm just going to start to sand it. I'm going to keep doing this. I'm going to work from different directions check on the progress of my sanding. You can see it's starting to sand down. I'm being careful not to scratch up the button so I'm holding it at an angle where my, it's a little hard to see in my towel, holding it at an angle where it's like this and not like that. So it's at a even plain. I'm just going to keep sanding. You can see I'm getting some of the metal dust and that's why you definitely have to wear your mask. I've sanded for about five minutes. You can see the shank is completely gone. It's smooth now. There are some scratches on the back of my button from where I sanded and that's going to be pretty hard to avoid just because you are wanting to sand that down so flush with the back you are going to scratch up the back side of the button probably a little bit. To me it's really no big deal. It's the backside. No one's going to see it. The important part is getting that completely smooth. So here's my front. Now Now I'm actually going to show you really quick just how to put on the ring form. I'm going to be using E6000, a wonderful glue. All I need to do to complete my ring is put a little bit of glue on that tab. Center that glue on tab in the middle of the back side of your button press into place and let dry and then you'll have a great ring. I hope this opens up a new world for you using buttons in jewelry making. Go to Beadaholique.com for all of your beading supply needs!
Related Videos


Bead Weaving Variation on Loops using Briolettes
Learn how to add loops to your bead weaving using a variety of beads including briolettes. This is a simple step to learn and can add lots of varie...
View full details
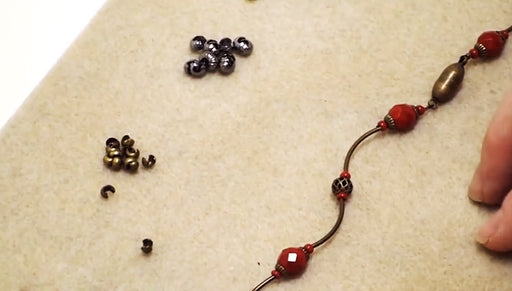
How to Use Crimp Covers
Cover your unsightly crimp beads with Crimp Covers. Gently squeeze shut around the crimped bead using crimping pliers. Can also be used to cover kn...
View full details
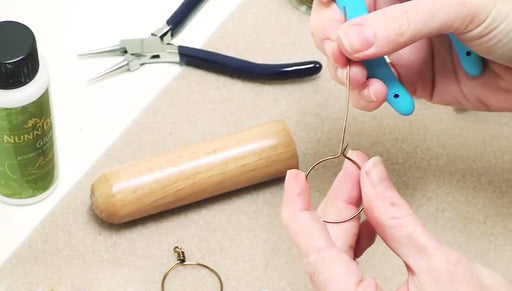
How to Make a Wire Wrapped Frame
Using either 16 or 18 gauge wire, learn how to make a wire frame by wire wrapping the wire around a form. After you have completed your frame, you ...
View full details